Новости, обзоры и акции
Подписка на прайс-лист
Каучук, резина и кабель КГ
Каучук как конструкционный материал стал доступен промышленности в конце 18 века, он был привезен в Европу с южноамериканского континента и представлял загустевший сок тропического растения — гевеи. Эластичность и водостойкость сразу сделали его востребованным, но широкому применению препятствовали использование дорогостоящего привозного натурального сырья и недолговечность изделий. Освоение в конце 19 века процесса вулканизации натурального каучука позволило преодолеть основные недостатки материала и спрос на продукт названный резиной вырос многократно.
Сущность вулканизации заключается в создании поперечных химических связей между линейными макромолекулами каучука, создание т.н. вулканизационной сетки, придающей материалу повышенную термоустойчивость, механическую прочность и долговечность. Изначально данный процесс реализовался при нагревании смеси натурального каучука, серы, а также дополнительных присадок и наполнителей непосредственно в момент формования изделия. В начале 20 века крупным потребителем материала стала военная отрасль, а также активно развивающаяся электротехника. Первая мировая война явилась стимулом для поисков альтернативных источников ценного материала, ставшего стратегическим — ни танк, ни самолет тех лет без него уже не могли обойтись... В 1926 году Советское правительство объявило всемирный конкурс на производство искусственного каучука. В мае 1928 года этот конкурс выиграл С. В. Лебедев. В качестве сырья он использовал обыкновенный картофель, из которого получал спирт, а уже из спирта — дивинил (бутадиен) продуктом полимеризации которого и является синтетический каучук (в данном случае СКБ). Из 1 л спирта он получал 50 гр дивинила. Таким образом на изготовление одной автомобильной шины уходило 500 кг картофеля. Позднее ученые нашли способ добычи дивинила из природных газов, а в 1932 году в Ярославле дал продукцию первый завод синтетического каучука. На втором месте по производству синтетических каучуков оказались немцы, которые активно готовились к войне. Их производство было налажено на заводе в городе Шкопау, который СССР после победы по условиям репараций вывез в Воронеж. Третьим производителем стали США: после захвата Японией в начале 1942-го года рынков природных каучуков поставки были приостановлены, в ответ правительство США менее чем за три года построило 51 завод. Дальнейшее развитие технологий потребовало новых марок резин: растущую энергетику, аэрокосмическую промышленность и ВПК не устраивали старые материалы, в связи с чем стали появляться резины на различной химической базе: уретановые, бутадиенстирольные, силоксановые, фторкаучуки и т.д., имеющие уникальные свойства и технологии переработки. Для их вулканизации требовалась уже не сера, а органические перекиси, синтетические смолы, нитросоединения и др., вулканизация также оказалась возможна под действием ионизирующей радиации. Высокая стоимость этих материалов ограничивала их применимость только специальными целями. Отчасти это диктовалось и качественным отставанием советской промышленности (в т.ч. химической) от капиталистического мира, текущие потребности экономики удовлетворялись за счет старых технологий - не лучших, но проверенных и не требующих капитальных вложений. В 70-80 годах 20 века именно они легли в основу ряда существующих поныне производств кабелей типа КГ и нормативной базы (ГОСТ 24334-80 принят как видно в 1980 году и на сегодня в части технологий материалов не соответствует реалиям жизни). Более технологичные и экологичные материалы для кабельной промышленности казались тогда делом отдаленного будущего. По ряду причин, выходящих за рамки данного текста, отдаленное будущее, о котором мечтали наши ученые, быстрее наступило в промышленно развитых капиталистических странах. С одной стороны этому способствовало ужесточение требований к кабельной продукции, с другой — рост требований к экологии и экономической эффективности её производства. Ответом на требования жизни стало появление высокоэластичных материалов и рецептур, имеющих упрощенную технологию переработки, максимально приближенную к пластмассам и ПВХ. Часто применяемое в отношении новых материалов слово «термоэластопласт» (ТЭП) не всегда верно по¬скольку по свойствам к термоэластопластам близки некоторые смеси полимеров с ограниченной совместимостью, термопластичные резины на основе композиций каучуков и термопластов, что делает классификацию данных групп материалов по формальным признакам затруднительной. В частности свойство частичной или полной обратимости состояния материала при его нагреве/охлаждении не является уникальным для ТЭП. Учитывая что развитие химии полимеров в последние десятилетия имеет взрывной характер (сравнимый с развитием электроники) считать сложившееся в технологии полимерных материалов положение окончатель¬ным не приходится, новые идеи и решения появляются постоянно. В современном мире нельзя позволить себе оставаться в стороне от прогресса: в 2008г. ООО «Конкорд» начало программу по мониторингу и изучению современных технологий и кабельных материалов на основе каучуков. Доступные на тот момент отечественные ТЭП не полностью устраивали, в связи с чем при предприятии была создана собственная исследовательская база и привлечены к разработкам профильные специалисты. Результатом этой работы стало появление уникальной рецептуры, позволяющей обеспечивать соответствие изделий всем нормированным электрическим и механическим параметрам. Основой её является стирол-бута-диен-стирольный каучук (БВБ) и комплекс присадок и добавок, обеспечивающих необходимые свойства. Вопрос: это резина или ТЭП? — в отношении применяемого материала имеет смысла не более чем: это медь или металл? — в отношении токопроводящих жил. Применяемый ООО «Конкорд» материал проявляет свойства термоэластопласта и изготовлен на основе синтетического каучука. Работа над улучшением его рецептуры продолжается, в частности для повышения его термостойкости.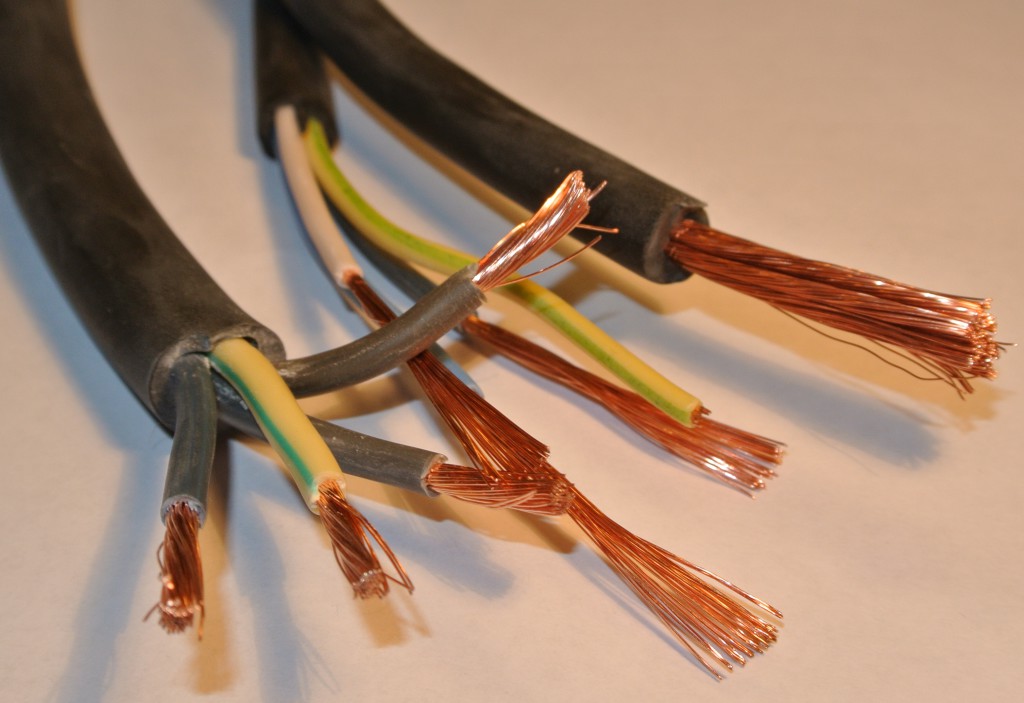
Полимерная композиция, применяемая ООО «Конкорд» для кабелей КГ обеспечивает нанесение покровов на изделия с минимальным эксцентриситетом, что позволяет снизить диаметр изделий и расход материалов не выходя при этом за минимальные допуски, что уменьшает горючую массу кабелей. Немаловажно что отсутствие соединений серы в покровах производимых кабелей позволяет токопроводящим жилам длительное время не окисляться, что делает их коммутацию гораздо более легкой и качественной. Также применяемый материал имеет хорошие показатели морозостойкости и легко переносит низкие температуры.
ООО «Конкорд» ведет мониторинг состояния образцов изделий с самого начала их выпуска и не располагает информацией о несоответствии применяемых материалов нормам безопасности, а также заявленным условиям и срокам эксплуатации. Статистика обращений потребителей, а также собственные исследования показывают что деструкция покровов производимых кабелей КГ происходит только при грубом нарушении условий их эксплуатации (перегрузка, интенсивная механическая нагрузка, эксплуатация в смотанном состоянии в сетях переменного тока). Гарантировать надежную работу изделий в недопустимых режимах не представляется возможным: если требуется некий запас по прочности и/или токовой нагрузке — необходимо применять кабель соответствующего номинала и конструкции (пусть и более дорогостоящего), а не рассчитывать на недокументированные возможности более дешевого изделия. В настоящее время ряд ведущих предприятий отрасли приступили к выпуску различных гибких кабелей КГ с покровами на основе ТЭП (на базе синтетических каучуков в т.ч.), успешно прошли сертификацию и предлагают свою продукцию на рынке — что подтверждает объективный характер происходящих процессов замещения материалов. Так же в своё время человечество отказалось от паровых машин, так же отказалось от радиоламп и отказывается сейчас от ламп накаливания — при этом сами идеи и технологии использования энергии пара или элетровакуумных приборов остаются актуальными и востребованными. Кто бы ни был производителем изделия и какие бы материалы для него ни применялись основным критерием качества является соответствие эксплуатационных и электрических параметров кабеля нормативной документации и его пригодность для применения по прямому назначению. Не существует правильных или неправильных материалов и технологий - важно соответствие результата техническим нормам. Есть все основания полагать, что массовый рынок силовых кабелей в дальнейшем всё больше будет уходить от применения диеновых резин в сторону более технологичных термоэластопластов (и родственных им материалов) на различной основе, при этом «классические» резины в качестве покровов кабелей также останутся востребованы на рынке, но сфера их применения вероятно ограничится изделиями специального назначения.